Productiebedrijven komen vaak in grote problemen als er een tekort is aan grondstoffen. Dat zagen we tijdens de pandemie en door de stremming van het Suezkanaal gebeurde dat weer. Ook de oorlog in Oekraïne zorgt voor problemen. Arno Kasper deed onderzoek naar hoe bedrijven hiermee omgaan, wat resulteerde in zijn proefschrift.
Een heel klein schokje in de keten kan zich uitbreiden tot een groot probleem: ‘Dat zag je duidelijk bij het chiptekort. Het begon bij computers waar geen chips voor waren, maar het breidde zich uit naar autofabrikanten en nog verder. De bron is wisselend, maar de gevolgen zijn altijd gelijk. Het tekort verspreidt zich over allerlei bedrijven. Hoe bedrijven daar het beste mee om kunnen gaan, was het topic van mijn onderzoek.’
Overleven van bedrijven
Het idee was altijd dat de productieketen daar op twee manieren mee om kan gaan; door buffers aan te leggen of door bridging. ‘In het eerste geval leg je voorraden aan of zet je extra personeel in. Dan kun je de schok opvangen zodra de materialen wel weer binnenkomen. Bridging is dat je gaat samenwerken met je leverancier of klant. Dat zijn wel heel algemene zaken. Ik keek naar wat bedrijven intern doen bij zulke tekorten. Bufferen is leuk, maar wat je niet hebt, heb je niet. Als je wel bufferde, raakt dat ook op. Als je leverancier het ook niet meer heeft, dan valt er weinig samen te werken. De problemen werden bij veel bedrijven zo lang mogelijk buiten de deur gehouden, maar toen dat niet meer ging, zag je iets interessants. Het probleem werd geaccepteerd en er werd gekeken naar wat de interne mogelijkheden waren.’
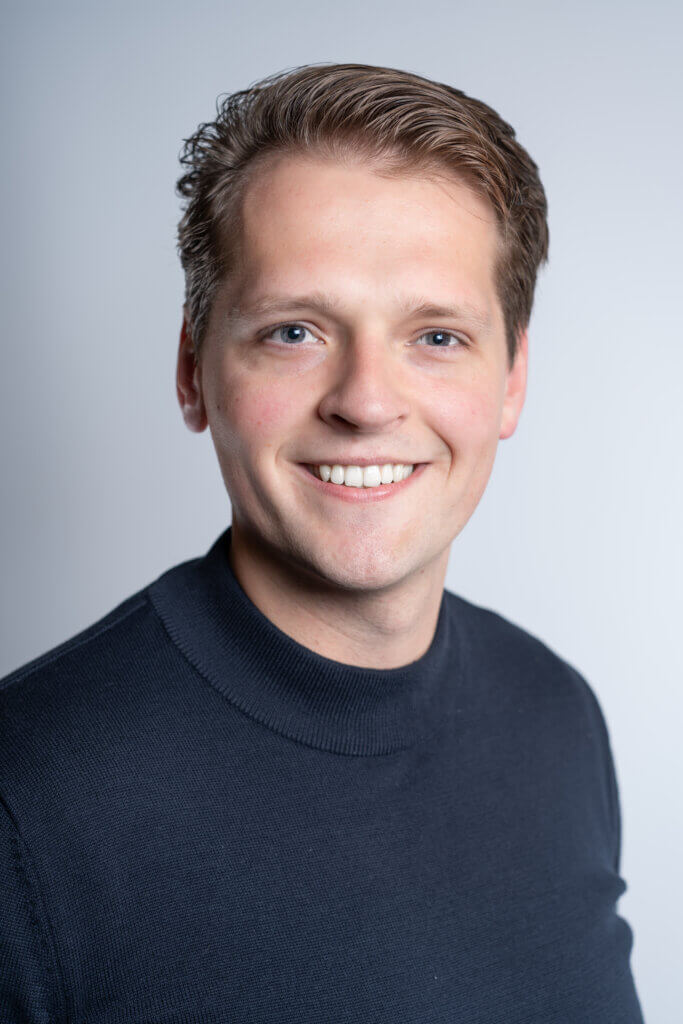
Wat kan wel?
Bedrijven reorganiseerden zichzelf. ‘Ze accepteerden dat ze de controle kwijt waren en dat het anders moest om een chaos te voorkomen. Dat maakte dat ze zichzelf anders gingen inrichten. “Dit is de situatie, wat kunnen we anders doen?”, vroegen de managers zich af. Eén van de cases in mijn onderzoek was dat ze een andere manier van plannen gingen toepassen en daarmee legden ze de puzzel een stuk nauwkeuriger. Wat is er wel? En wat is wel mogelijk? Dat maakte dat dit bedrijf voorkwam dat het chaos werd en uiteindelijk leerde om ermee om te gaan, ook al was het moeilijk. In plaats van een product eerst te bedenken en dan de overdracht naar productie te doen, werd gekeken naar de alternatieve mogelijkheden voor de productie. Kunnen we dit product in plaats van met plastic ook met een ander materiaal maken? Wat heeft dat dan voor gevolgen voor de engineering? Of kunnen we het product aanpassen aan wat wel mogelijk is, bijvoorbeeld door het kleiner te maken? Is de klant daarmee akkoord? Kunnen we het dan op die manier produceren?’
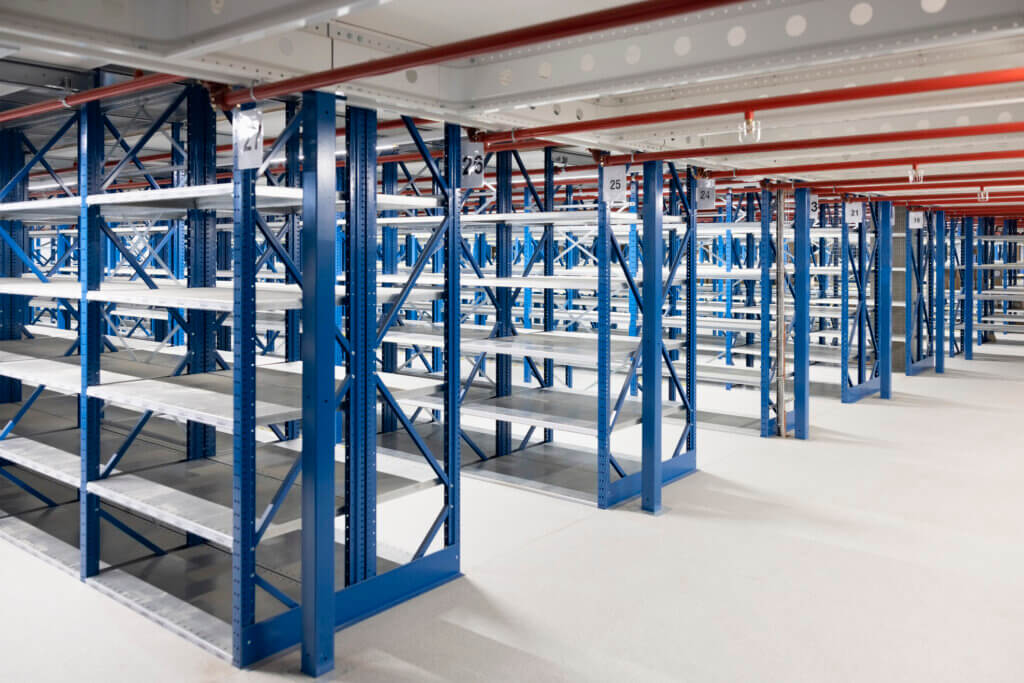
Impact op de productieplanning
Dit heeft een enorme impact op de productieplanning binnen een bedrijf. Dit doet niemand zomaar, want dit vraagt om een mini-reorganisatie en geen enkele directeur staat daarom te springen. Dat vraagt lef en inzicht, maar vooral om veel durf, maar het leverde wel veel op. Door deze veranderingen viel de logica om de productie buiten de deur te houden, helemaal weg. ‘Dat was heel opvallend’, zegt Kasper. ‘Het was niet de allerbeste oplossing, maar gegeven de situatie, was dit wel het beste dat een bedrijf kon doen. Dit was niet iets waar ze zelf voor gekozen hadden, maar het maakte wel dat bedrijven niet helemaal met hun handen in het haar zaten.’
Ervaring binnen het bedrijf
Ditzelfde gebeurde bij personeelstekorten. Probeer je gewoon door te gaan als voorheen als bedrijf of beweeg je mee met de situatie? ‘Gedurende tweeëneenhalf tot drie jaar volgde ik meerdere casebedrijven. Enerzijds zagen we perioden dat de directie probeerde interne veranderingen zo lang mogelijk tegen te houden. Uiteindelijk werd die gedragsverandering wel geforceerd door de omstandigheden. Er was geen ontkomen meer aan. Ze hadden geen keuze meer, het was veranderen of het bedrijf ging failliet. Anderzijds zag je dat bedrijven met ervaring het meer zagen aankomen en daardoor ging het daar eenvoudiger. Maar het was nog steeds een enorme switch voor iedereen, naar een andere manier van werken. Dat maakt dat je als bedrijf de grip houdt. Die aanpassingen zorgden voor flinke sprongen in innovatie doordat productiebedrijven kijken naar andere manieren van werken en andere materialen. Dat kan voor blijvende verandering zorgen en het maakt bedrijven ook flexibel om met een nieuwe tegenslagen om te gaan.’ In de wetenschap bestaat het idee dat bedrijven weer terugkeren naar hun oude processen zodra dat mogelijk is, maar Kasper zag dat helemaal niet. ‘Er waren juist blijvende veranderingen door interne ingrepen.’
Personeel meenemen in het proces
Door personeel mee te nemen in de situatie, laat je zien wat niet meer kan en wat er voor alternatieven zijn. Daar zijn de meeste mensen wel toe bereid. ‘Een bedrijf waar ze bussen maken, had heel veel problemen door het materiaaltekort. Als er geen alternatieven voorhanden zijn, dan zijn er andere oplossingen nodig. Leveranciers konden hogere eisen stellen, zoals eerst betalen en over een jaar pas levering. Daarnaast werd op een andere manier gewerkt. Niet meer allemaal dezelfde lampjes voor een klant, maar verschillende lampjes. Niet meer de vraag of je die banden wel op tijd krijgt, maar de vraag of je die materialen voor die specifieke bestelling wel op tijd krijgt. Dat is een andere manier van werken. Een inkoper is doorgaans niet direct bij klanten betrokken, maar op een gegeven moment dan wel. Daarom is het ook belangrijk om je personeel mee te nemen in het proces van de verandering. Je laat ze zien hoe je nog wel kunt leveren.’
Florerende bedrijven
Kasper ontdekte dat een aantal bedrijven juist heel erg floreerde tijdens de pandemie toen hij dit onderzoek deed. Bijvoorbeeld bedrijven in medische apparatuur of de makers van mondkapjes. Ook bedrijven die voldoende op voorraad hadden of die net goede contracten hadden afgesloten, deden het prima. ‘Daar was moeilijk een lijn op te trekken. Goede externe afspraken bijvoorbeeld of meerdere suppliers en het risico actief managen. Maar dat is bijna niet dicht te timmeren. Als je geluk hebt, rol je erdoorheen. Soms hadden bedrijven net niet datgene nodig waar een tekort aan was. Ik kwam ook bij bedrijven waarvan ik verwachtte dat er geen problemen zouden zijn, waar er dan maar één klein onderdeel niet op voorraad was en ook niet leverbaar was, die hadden de andere negenennegentig onderdelen op voorraad, maar net door dat ene liep alles vast. Andere bedrijven waarvan ik wel verwachtte dat die het moeilijk zouden hebben, gingen fluitend door, omdat zij extern goede afspraken hadden gemaakt. Het is lastig te voorspellen welke bedrijven een probleem zullen krijgen.’
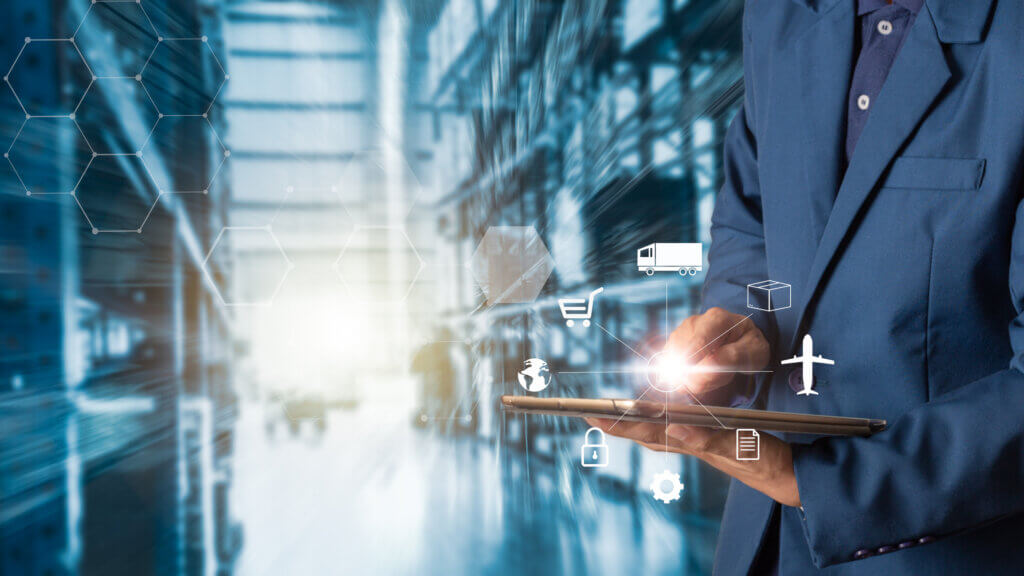
Vierde industriële revolutie
De computer speelt al heel lang een grote rol in de maakindustrie, maar er ontstaan steeds meer mogelijkheden door nieuwe ontwikkelingen. ‘Diverse afdelingen binnen bedrijven werken heel geautomatiseerd, maar je ziet vaak dat er nog een groot gat zit tussen wat er op kantoor gebeurt en de werkvloer. Dat gat wordt steeds meer gedicht. Waar het voorheen losstaande onderdelen waren, zoals een mixer in een keuken, wordt de mens en machine steeds vaker slim verbonden met de rest van de werkvloer. Daardoor ontstaat een netwerk binnen een fabriek en werkt iedereen samen in het fabricageproces, de een als mens en de ander als machine. Dat wordt wel de vierde industriële revolutie genoemd. Producten moeten nog steeds gemaakt worden, dat verandert niet, maar de manier waarop dat gebeurt veranderd wel. Werknemers zijn nu vaak een stuk hoger opgeleid dan vroeger. Mede daardoor worden machines ook steeds slimmer en met elkaar verbonden, waardoor dynamische samenwerking mogelijk is. Dat zorgt ook weer voor meer overleg en meer gelijkheid. Vooral in Nederland worden structuren platter, dat is zeker nodig als er door tekorten een verandering in de productie of zelfs alleen de volgorde van productie moet komen.’
Op grote schaal produceren
Puur het ontwikkelen van de technologie is niet genoeg, er zullen altijd mensen nodig zijn die beslissen hoe je gaat produceren. Veel startups willen flink opschalen, maar daar is kennis voor nodig die grotendeels verdwenen is uit Europa. ‘Batterijfabrikanten lopen daar tegenaan. Ze weten hoe ze een batterij moeten maken, maar om het op grote schaal en goedkoop te produceren, dat is weer een ander verhaal. Dan verlies je die strijd en dat is heel jammer. Je kunt je niet alleen op het maken van de beste producten richten, maar die stap naar snel en goedkoop produceren vraagt wat andere kennis. Die is niet zo veel meer voorradig, mede omdat veel producten buiten Europa worden gefabriceerd. Als je de onderdelen hebt om iets te produceren, wil dat niet zeggen dat je dat dan ook kunt maken.’